Selecting Irradiance Control Points in Weathering Testing
Blog
Last Updated 2025
In weathering and lightfastness testing, selecting the appropriate irradiance control point is essential for accurate results. Irradiance, expressed as the radiant power of light per unit area, is specified in test standards as a magnitude at a particular wavelength or wavelength range. For instance, ASTM G154 Cycle 1 for UV exposures requires 0.89 W/m²/nm at 340 nm, while ASTM G155 Cycle 5 for Xenon-arc exposures calls for 1.10 W/m²/nm at 420 nm. Some standards use total ultraviolet (TUV, 300–400 nm) control, or even a broader “UV+Visible” range (300–800 nm). But the question is, how do you choose the best control point?
In fluorescent UV testing using QUV testers, the narrow-band control wavelength depends on the lamp type. UVA-340 lamps peak near 340 nm, making it a natural control point, while UVB-313 lamps are controlled at 310 nm peak because the peak at 313 nm is an artifact of a mercury phosphor and may not always be representative of the lamp’s irradiance. UVA-351 lamps, despite peaking near 351 nm, are controlled at 340 nm for consistency and calibration simplicity, as specified in ISO 4892-3 Cycle 5. UVC-254 lamps concentrate all of their output at 254 nm, so the decision of control wavelength is a trivial one! TUV-421 lamps have a broader spectrum through the UV region and even the visible, so TUV (300-400 nm) control is selected.
For Q-SUN xenon-arc testers, the narrow-band control point is chosen based on the optical filter, and the objective of the test focus. Daylight filters, used for outdoor materials typically sensitive to UV light, typically use a 340 nm control point, ensuring spectral tability in the UV region as lamps age. Window filters, suited for indoor materials affected by longer-wavelength UV or visible light, often use a 420 nm control point, since irradiance at 340 nm may be low. However, there is flexibility — Daylight filters can use 420 nm control, and Window filters (except Window-IR) can use 340 nm, depending on the application.
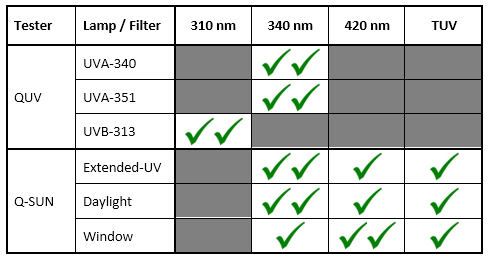
Table 1. Irradiance control wavelengths. Double-green check marks indicate control point is available and most commonly used – a single green check indicates that the control point is available, and valid, but less commonly used.
TUV control (300–400 nm) offers a compromise, capturing total UV irradiance as a balance between 340 nm and 420 nm. TUV control is specified in many ISO and European standards, and is a good choice when the spectral sensitivity of the material under test is not known. All Q-SUN testers offer 340 nm, 420 nm, and TUV control; the Xe-8 model features all three standard as part of the onboard sensor array.
Spectral power distribution (SPD) data, available on Q-Portal for all of Q-Lab's optical filters and lamps, enables conversion between different setpoints. This data can also be used to calculates exposure durations to achieve specific radiant exposures (in MJ or kJ).
The use of so-called "UV+visible" or "global" control wavelength ranges (300-800 nm or 300–3000 nm) are not recommended by Q-Lab for several reasons. Both of these ranges give too much weight to the visible and IR components of light, which are not nearly as important for materials durability as UV light. Additionally, measurement of irradiance above 1000 nm is very difficult, which can introduce additional error into measurement.
In conclusion, choose an irradiance control point based on lamp or filter type and the material’s sensitivity. QUV lamps always use a control point relevant to that lamp's output. Xenon lamps can be controlled using narrow-band (340 nm or 420 nm) or broadband (TUV) irradiance, depending on the requirements of the test standard.
Ready to get your testing program underway? Contact our team of experts today!